Customization Available
Application in Pig Iron Production (Blast Furnace Ironmaking)
Core Functions
Fuel & Heat Source: Metallurgical coke generates heat through combustion (furnace temperatures up to 2000°C), creating the high-temperature environment required for iron ore reduction.
Reductant: Carbon in coke reacts with iron oxides (e.g., Fe₂O₃) to produce CO, which reduces iron oxides to metallic iron (reaction: Fe₂O₃ + 3CO → 2Fe + 3CO₂).
Structural Support: Coke particles form a permeable structure in the blast furnace, maintaining gas flow and preventing clogging from molten slag.
Quality Requirements
Low sulfur (≤0.7%), low ash content (≤12%), and high fixed carbon (>85%) are critical to minimize slag formation and improve iron purity. For example, a 0.1% increase in sulfur raises coke consumption by 1.8% and reduces blast furnace output by 1.5–2.0%.
Substitutes and Limitations
Modern techniques (e.g., coal injection, oxygen enrichment) can partially replace coke (up to 50% substitution), but coke remains irreplaceable as a structural support and primary reductant.
Application in Steelmaking
Converter and Electric Arc Furnace (EAF) Processes
Converter Steelmaking: Coke serves as an auxiliary fuel and carbon source, aiding in desulfurization, dephosphorization, and carburization of molten steel. For instance, CO generated from coke combustion adjusts the furnace’s oxidizing atmosphere.
EAF Steelmaking: Coke supplements heat in scrap metal melting, providing carbon to stabilize steel composition and oxidize impurities.
Indirect Impact
High ash content in coke increases impurities in steel, necessitating additional refining steps (e.g., LF refining, RH vacuum treatment).
Application in Metal Recycling
Non-Ferrous Metal Smelting
Coke acts as a reductant and heat source in blast furnaces for copper, lead, and zinc production. For example, it reduces CuO to metallic copper (CuO + C → Cu + CO↑) and maintains temperatures of 1200–1300°C.
Solid Waste Recycling
Coke participates in carbothermal reduction to recover metals from metallurgical slags (e.g., extracting Fe-Cu-Mn-P alloys from copper slag).
Environmental Integration
Coke-derived materials (e.g., activated coke) are used for flue gas desulfurization and wastewater treatment, supporting sustainable metal recycling.
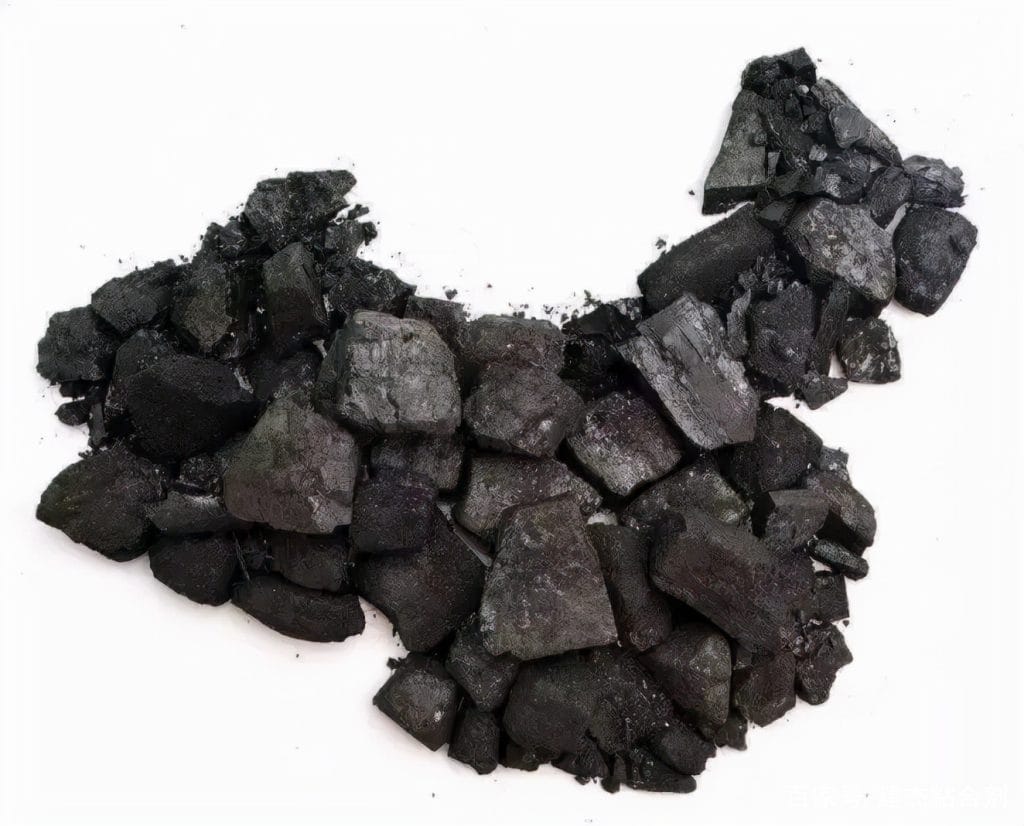
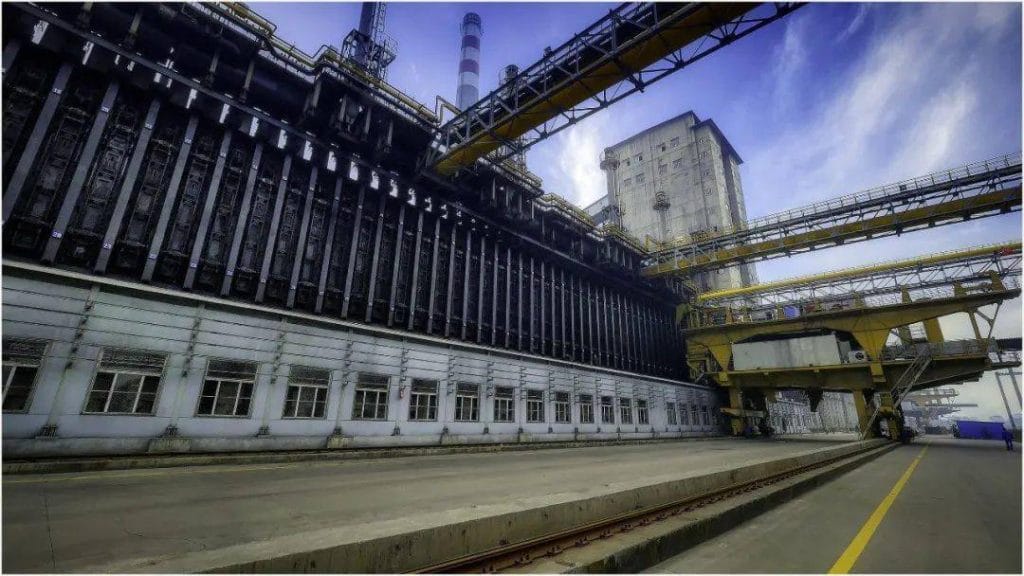
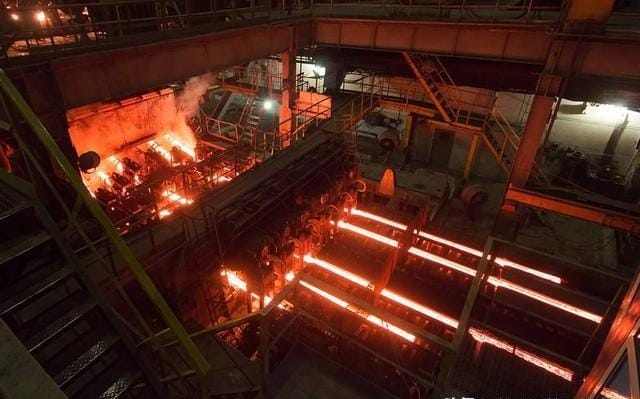
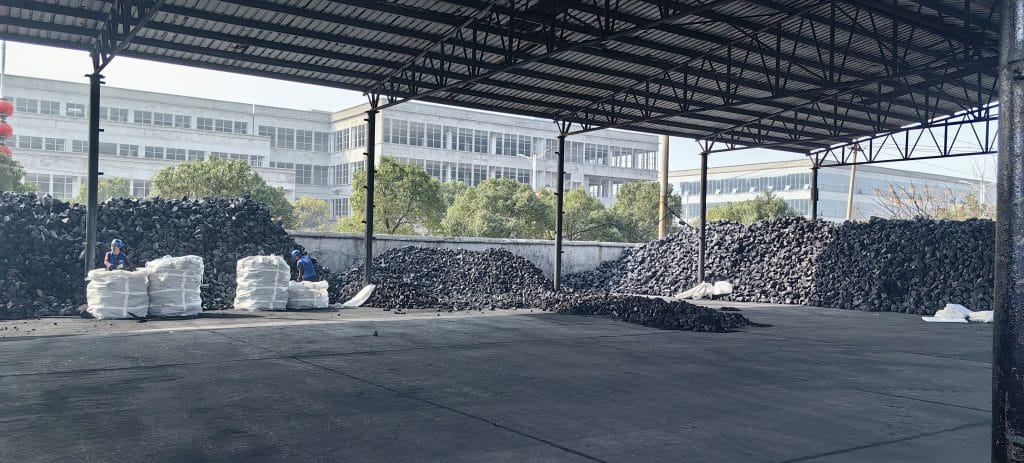
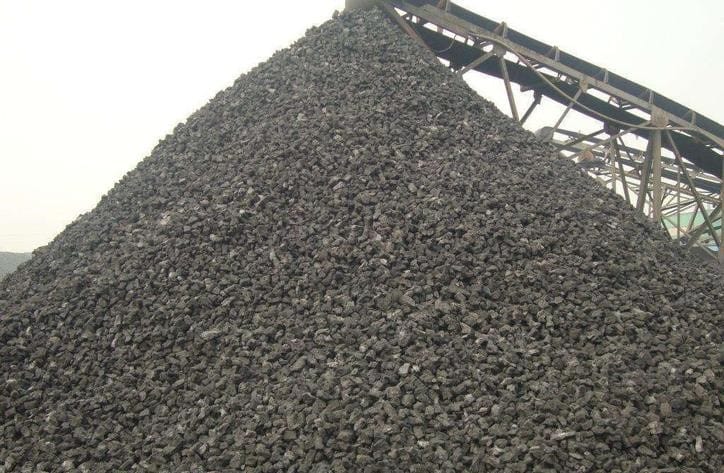
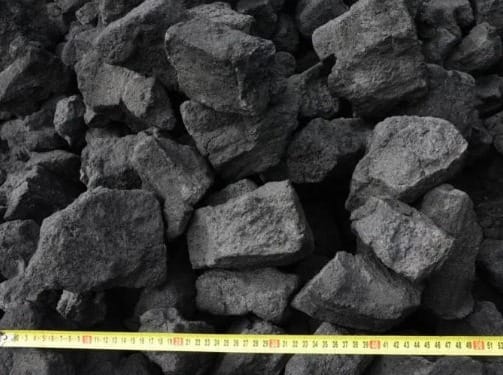
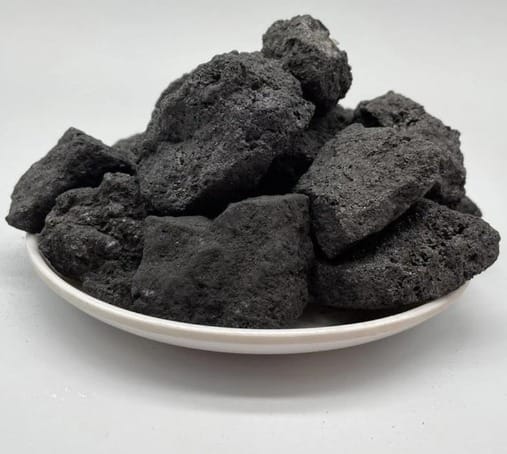
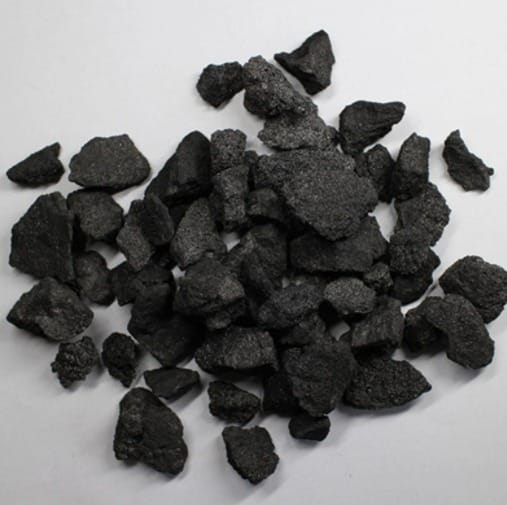
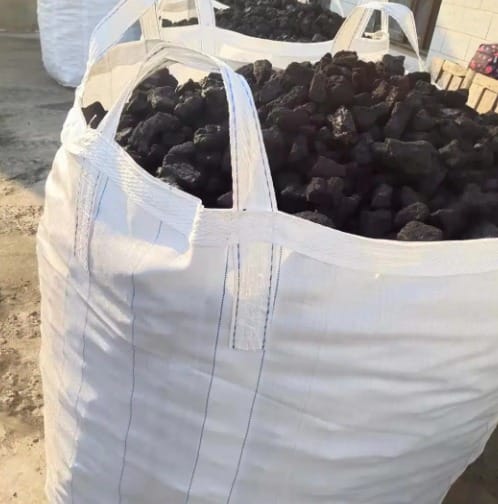
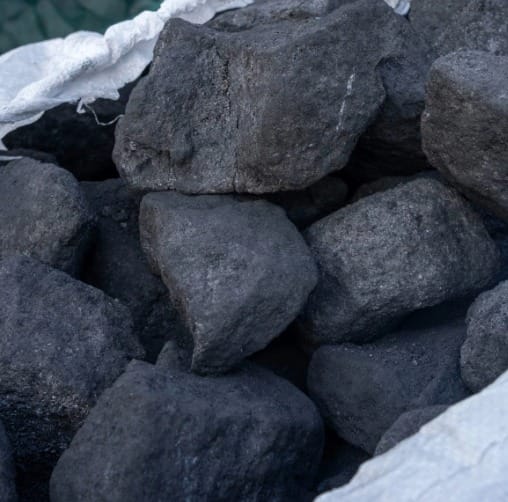